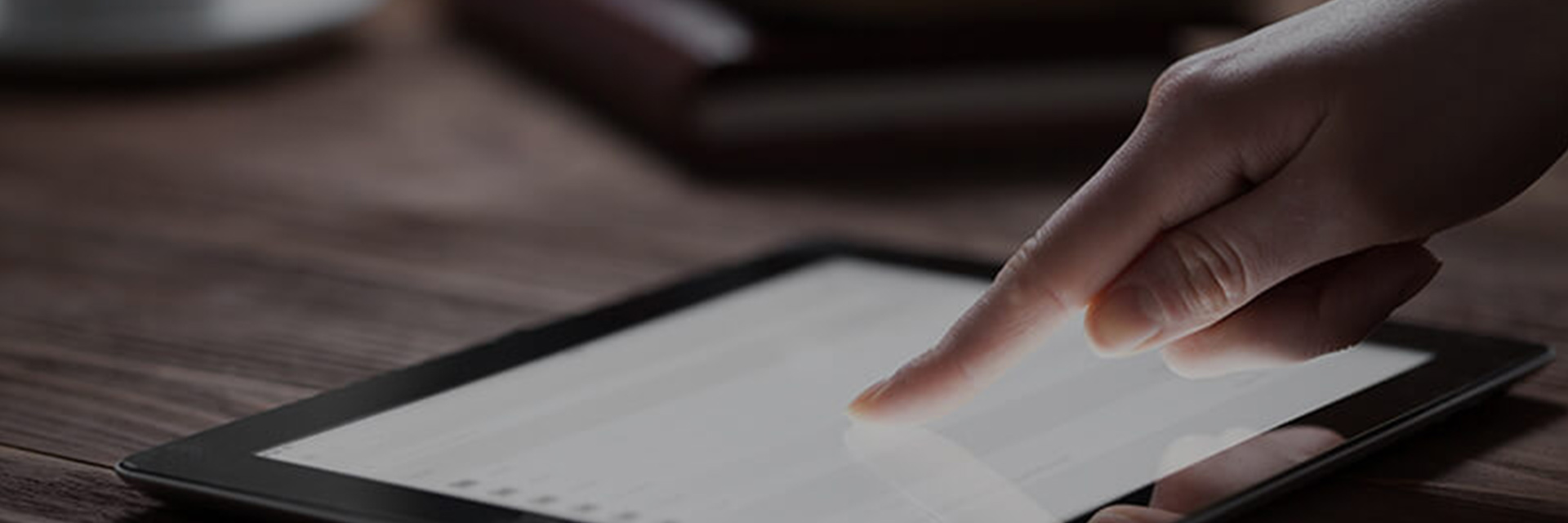
Fritz Metzger ist seit Februar 2021 bei Berylls by AlixPartners (ehemals Berylls Strategy Advisors) tätig, einer internationalen und auf die Automobilitätsindustrie spezialisierten Strategieberatung. Er ist Experte für Automotive Operations.
Seit 2011 fokussiert er dabei strategische Ausrichtung und Effizienzsteigerung der Operations von Automobilherstellern und -zulieferern. Zudem berät er das Top Management in kritischen Situationen, dazu gehören Task Forces im Rahmen der Entwicklung und Industrialisierung, Verlagerungen und die Restrukturierung von Werken und kompletten Zulieferern. Die Herausforderungen der E-Mobilität sind dabei stets im Blickfeld.
Vor seiner Zeit bei Berylls war er als Direktor bei internationalen Strategieberater PwC Strategy& tätig, sowie als Vertriebs- und Projektleiter bei einem mittelständischen Zulieferer und Maschinenbauer.
Fritz Metzger ist ausgebildeter Wirtschaftsingenieur mit einem Abschluss von der ESB Business School Reutlingen und hat einen MBA an der Universität Salzburg absolviert.